A etapa de fragmentação de minérios tem por objetivo utilizar diferentes técnicas e equipamentos (que serão citados a seguir) para reduzir o material vindo da mina até um tamanho que possa ser prosseguido o beneficiamento. Geralmente a cominuição é a primeira etapa do tratamento de minérios e visa, a partir de uma rocha, liberar o mineral valioso do mineral de ganga (sem valor) e, a partir daí, reduzi-lo até o tamanho desejado.
A fragmentação de rochas ou minérios é um processo que pode ser muito extenso e ter várias etapas até sua conclusão. O início desse processo é desde a fase do desmonte da rocha na lavra, em que são gerados os primeiros blocos que devem ter um tamanho ideal para que se possa prosseguir para a fase de britagem. Para evitar maiores gastos, o desmonte deve ser realizado com a maior eficiência possível, utilizando os explosivos ideais para o material em questão.
Britagem
A partir desse material vindo da mina, a primeira operação a ser realizada é a britagem, que fragmenta esses blocos utilizando britadores até que sejam reduzidos a uma fração que permita ser feita a moagem do minério. A britagem pode ser composta, também, por múltiplas etapas (primária, secundária, terciária e até quartenária) dependendo do material britado e para cada um desses estágios, podem ser usados diferentes britadores.
Na britagem primária, a razão de redução é em torno de um 1:8 com tamanho máximo na alimentação de 1000 mm e tamanho máximo na produção de 100 mm. Se caracteriza por operar em circuito aberto, sem descarte da fração fina (escalpe) da alimentação e emprega britadores de grande porte. Os britadores que podem ser citados nessa fase são: O britador de mandíbulas, britador giratório, britador de impacto e o britador de rolos dentado.
A britagem secundária pode ser também considerada o conjunto de todas as britagens posteriores à primária. Essa fase se caracteriza por ter o descarte prévio da fração fina na alimentação para aumentar a produção e os britadores utilizados são: britador giratório secundário, britador de mandíbulas secundário, britador cônico, britador de martelos, britador de rolos. Além disso, nessa etapa o tamanho máximo na alimentação é em torno de 100 mm e o tamanho máximo na produção 10 mm.
Geralmente o último estágio de britagem é a terciária, que tem o tamanho máximo na alimentação de 10 mm e o tamanho máximo na produção de 1 mm. A razão de redução geralmente gira em torno de 4:1 ou 6:1 e comumente são empregados os britadores cônicos que trabalham em circuito fechado.
A britagem quartenária normalmente não é necessária, mas dependendo da empresa e do material que é fragmentado, ela é realizada. É uma fase que exige enorme controle de operação, então também é feita em circuito fechado e tem o tamanho máximo na alimentação de 5 mm e tamanho máximo na produção de 0,8 mm.
Britadores
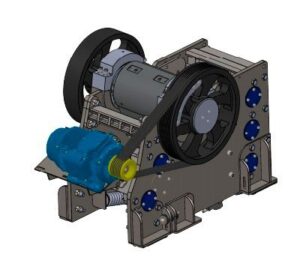
Moagem
Nessa etapa, a última da fragmentação de minérios, são trabalhados os materiais finos vindos da britagem para que sejam reduzidos ao tamanho adequado para a concentração do minério. As partículas são reduzidas por impacto, compressão, abrasão e atrito para que seja o mineral de interesse seja liberado para as próximas fases.
A depender do material e da operação da usina, serão empregados diferentes tipos de moinhos. Os que são mais utilizados são: os moinhos cilíndricos, que pode ser de barras, de bolas ou seixos, moinho de martelos, dentre outros.
Moinhos
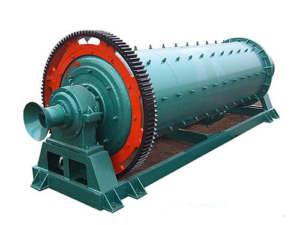
Referências bibliográficas
LUZ, A. B.; FIGUEIRA, H. V. O.; Almeida, S. L. M. Tratamento de Minérios. CETEM/MCT: 2010.
Créditos da capa para AMC – Mining & Crushing. Disponível em: https://www.africanminingandcrushing.com/. Acesso em: 12 nov. 2020.
Material muito bom